MANAGING THE SUPPLY CHAIN DURING A PANDEMIC-CRISIS AND RECOVERY
MANAGING THE SUPPLY CHAIN DURING A PANDEMIC – CRISIS AND RECOVERY
Posted By: Missy Weiss, CEO July 25, 2020
The impact of the Covid-19 pandemic on the aerospace industry will be more extensive than previous downturns as air travel in the U.S. alone has dropped by as much as 95%. Supply Chain Managers must proactively map the path for their organization through the emerging supplier landscape.
As regions, states, and municipalities implement a phased approach to re-opening after the Covid-19 pandemic, business will not be returning to normal anytime soon. Fear of enclosed group spaces, increased use of telecommunications for business meetings, and an astronomical unemployment rate are significant factors that only add to doubts about when travelers will return to the air and the commercial aerospace industry will recover.
Not all OEM's are affected to the same extent. Those with government contracts are less likely to see any demand impact at all. However, whether directly impacted or not, aerospace OEM's need to manage through the resulting supply chain crisis while also planning for a changed industry as recovery begins

According to Airlines for America, a trade group representing the largest US carriers, as of April 15th, 2020 U.S. airlines had idled 2700 planes, representing more than 44% of their fleet. This reduction in passenger volume along with the uncertainty about when it will rebound is causing airlines to defer delivery of new aircraft, thus forcing OEMs to lower production rates. This sharp rate reduction ripples through the entire supply chain down to the smallest suppliers.
While U.S. defense companies demand is protected by DOD purchasing, they will experience supply chain disruptions as their suppliers – many of whom also do work for commercial aerospace companies -- face operational and financial struggles of their own due to the virus.
Amid disruptions to the supply chain caused by the pandemic, classic ERP systems with normal lead time planning and order release will not work. As suppliers manage costs and cash during this time of uncertain demand, the historical focus on efficiency and low cost will not be sufficient to minimize operational risks.
To keep manufacturing operations going without interruptions, organizational leaders will need to continually reevaluate inventory buffers based on greatest risks. Supply Chain leaders have an important role to play in their organizations by identifying supply risks and developing plans to minimize any impact to operations.
There are two phases Supply Chain Management organizations will need to manage through – The Crisis Phase, and The Recovery Phase.
THE CRISIS PHASE
The focus of management during the Crisis Phase should be understanding the immediate impacts upon their supplier landscape and continually monitoring and responding to the spikes and disruptions that are inevitable until a vaccine and/or therapeutic drugs are widely available.
The Silent Threat of Low Global Demand
Companies that are fortunate enough to maintain their operations during the pandemic need to be aware of the potentially devastating impact it has had on other markets served by their suppliers.
In the very short-term, buying organizations can be lulled into complacency because their supply chain actually seems better than ever as their suppliers are able to focus on the few customers that are still giving them orders. Of course, it is inevitable such “houses of cards” will come crashing down as the suppliers’ over-all operations and finances are affected by the economic downturn and they are less able or unable to meet any of their commitments.
If Supply Chain Managers just “wait for the call” from a problem supplier – or even a supplier that has never before been a problem -- they may find it difficult or impossible to recover when issues emerge.
The worst call, of course, is the call that never comes… because a supplier has totally succumbed to the tragic economic environment caused by the pandemic.
In order to avoid traumatic and sudden surprises from their suppliers, Supply Chain Managers have no choice but to carefully develop a Supply Chain Map.
Mapping the Supply Chain
The Supply Chain Map is a total assessment and management plan for a supply base.
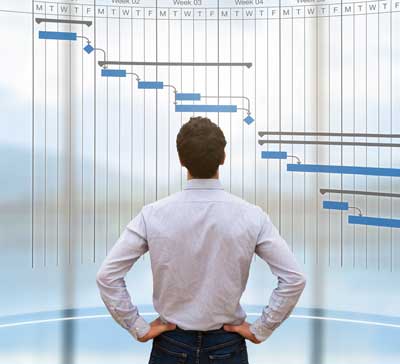
Mapping must include all suppliers and parts from the very largest to the very smallest. This includes hardware, connectors, components, and special processes. The smallest items are often overlooked, and they can shut down your operations.
Key Evaluation Elements in a Supply Chain Map:
- How much inventory does the supplier have? (Finished Goods, WIP, components, raw material)
- What percent of revenue has the supplier lost due to recent events?
- What is the supplier’s financial situation? Are they at risk of bankruptcy? Are they paying their suppliers? Do they have cash available to purchase raw material when needed?
- Is the supplier’s viability being artificially sustained by PPP funding? Is a cliff coming when that runs out?
- Has the supplier responded appropriately to the pandemic? Are they practicing safe work guidelines recommended by the CDC to minimize risk in the workplace?
- In cases where they have been impacted by supply issues or the pandemic, do they have a recovery plan and what is the timeline for the plan?
- Have key personnel at the supplier been recently laid-off? Have key personnel at the OEM, who worked closely with the supplier recently been laid-off?
- If the supplier does not make it through the economic crisis, are there abundant and ready alternative suppliers?
For OEMs and large system manufacturers, creating a comprehensive supply chain map is a big task. To maintain visibility and to drive results, a centralized area (“War Room”) should be established along with frequent management reviews and collaborative problem solving efforts.
Once mapping is complete, supply chain leaders need to evaluate critical suppliers in terms of “time to impact” on their company’s operations and establish immediate solutions to eliminate, minimize, or defer the most rapidly emerging problems – short term supply chain survival tools.
Short Term Supply Chain Survival Tools:
- Increased Inventory: Organizations will need to evaluate carrying more inventory to buffer ongoing disruptions in the supply chain and the transportation system.
- Second Sourcing: Alternative suppliers need to be identified and vetted, and in some cases investment needs to be made in dual tooling to ensure uninterrupted supply. This might be required even in cases where one or two suppliers have a long relationship and reputation for stability that has “protected” them from dual sourcing in the past.
- Financial Assistance: In some cases a great supplier might just need help “staying afloat” during these difficult times. Although it goes against the trend in recent years of “pushing down” financial responsibility, organizations might find that the only way to keep their supply base in tact is to ease pressure on supplier cash flow with techniques such as reduced payment terms and customer purchased raw material.
Stay in Touch
It is always important to stay in touch with suppliers, but never more so than during this time of inherent instability and rapid changes in the business landscape.
In the Crisis Phase it is critical to frequently contact suppliers and update any changes from the original assessment. This is especially true when the Supply Chain Management organization has itself experienced reductions in force and thereby lost some of its “ears to ground” that would normally have been the early warning system for suppliers in trouble.
Senior supply chain leaders need to consciously increase their personal interaction with critical and high risk suppliers, as identified by the Supply Chain Mapping process, to build relationships and to encourage transparency and communication flow.
See For Yourself
In the case of critical or troubled suppliers, there is no substitute for “laying eyes” on the operation. Consistent in-person communication builds critical relationships and helps supply chain organizations get ahead of potential risks.
Although it is difficult to travel during the pandemic, efforts should be made to have a company employees or representatives visit critical and high risk suppliers to monitor what is actually happening.
Companies that are discouraging non-essential travel, or those that have reduced their internal supplier management ranks, should get assistance from firms that provide local resources near their high risk suppliers. Such firms can help with the initial mapping and also follow up regularly to verify information is still accurate and to check ”conditions on the ground”.
THE RECOVERY PHASE
In the recovery phase, the focus shifts to increasing production schedules as commercial air travel and associated product demand resumes. Challenges will emerge as OEM’s realize the damage their supply chain has quietly sustained while global product demand was low.
Before the pandemic, there were already capacity issues in the Aerospace industry due to the latest industry downturn. As the commercial market re-emerges after the pandemic, the ability for the supply base to support will be further diminished.

Suppliers facing reduced economies of scale will find it challenging, as always, to shed fixed costs. This financial distress will likely lead to some bankruptcies and liquidations, and in other cases there will be mergers and consolidations. All of this turmoil and change will result in further decreases in industry capacity.
Supply chain organizations will need to utilize their mapping intelligence and rely heavily on their supplier development groups to evaluate their suppliers’ current capacity and surge capability. The map developed for survival purposes during the Crisis Phase will need to be transformed to a plan for the return to stability and normal supplier relationships.
What were “second sources” will in some cases wind up as “primary sources” (or even “sole sources”) due to liquidations and mergers. Establishing new and productive relationships with these entities will be critical to supply chain performance.
Fiscal performance requirements will re-emerge also, which will add more pressure to Supply Chain organizations to return to reduced inventories and expanded payment terms.
The extent to which organizations are able to thrive during the recovery will be determined by the quality of the mapping and assessment they performed during the crisis.
Preferred Procurement Solutions
PPS is a supply chain services company with resources available to quickly assist organizations in mapping their supply chain and with follow up field support as the business climate recovers.
Our resources are deployed across the United States and internationally to provide localized supplier support without adding to your payroll while keeping travel cost and exposure low.
Contact us to discuss your needs and how we can help!