Travel Restrictions
TRAVEL RESTRICTIONS IMPACT SUPPLIER RECOVERY EFFORTS
Posted By: Missy Weiss, CEO September 4, 2020
Emergency supplier problems have never been easy to deal with, but ever changing domestic and international travel restrictions have made it even more difficult for procurement managers to respond. Smart organizations can get ahead of potential issues by carefully monitoring and planning for travel to distant suppliers.
Supply chain disruptions have been rippling through American industry since the onset of the Covid-19 pandemic. Such troubles are increasing as the government Payroll Protection Program (PPP) ends and key employees are laid off at suppliers.

Hidden Problems in the Supply Chain
OEM’s that maintained demand during the initial phases of the pandemic are being jolted as their suppliers face sudden financial and operational difficulties. This is especially true for government contractors that utilize suppliers who also service commercial clients. Many of these suppliers kept a portion of their staff on-board only while the government subsidized them through the PPP. Since production capacity has also been plentiful, customers have basked in a highly responsive supply environment as suppliers have been eager and able to get invoiceable orders out the door quickly.
Government support programs were intended to “bridge the gap” until the economy itself could support pre-Covid workforce levels, but the virus has proven too persistent – and the gap too wide, so workforces are being slashed dramatically at the expense of delivery performance. In some cases suppliers cannot maintain operations at all and are closing their doors with little or no warning.
Travel Difficulties
Over the past several years, while supply chains were running smoothly, procurement professionals have been able to minimize physical travel to suppliers by using modern communication technology such as phone calls, emails, and video conferences. However, in the case of suddenly emergent supplier issues, it has always been critical to get “boots on the ground” to assess situations, convey urgency, command attention, and resolve problems. In the most severe cases, re-sourcing of components can be necessary, which requires visits to new suppliers. Covid-19 has hampered the ability to respond this way by complicating, reducing, or eliminating the ability to travel freely to distant locations.
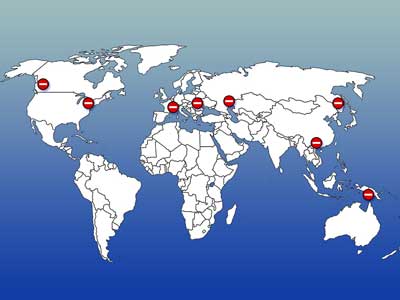
In addition to international travel restrictions that have been in place since early in the pandemic, several states have recently implemented rules requiring a 14-day quarantine for visitors from other “hot spot” states. These restrictions are especially jarring because a US passport has historically met little resistance anywhere in the world, and a key strength of the nation’s domestic manufacturing base has been its frictionless interstate commerce system.
Although individuals might take state quarantine rules lightly because they are difficult to enforce, businesses risk fines and liability if they direct or allow their employees to flout lawfully established rules. So, in cases where a long quarantine is required, unplanned business travel is essentially impossible.
Beyond government restrictions, many companies have instituted self-declared moratoriums on all but essential business travel to protect their employees and other stakeholders.
Some employees are themselves reluctant – or unwilling – to travel due to fear of getting sick or in consideration of their susceptibility to severe outcomes due to factors such as age or pre-existing health conditions. Others don’t want to travel because they are in frequent contact with friends or relatives who are old or have their own pre-existing conditions.
Pro-Active Planning During the Pandemic
Travel difficulties during the pandemic make it necessary for procurement organizations to acutely heighten their awareness of any trouble signs at distant suppliers and to have a plan for how to physically access them in case of an emergency. The following steps should be taken to make sure supply chain disruptions can be dealt with during these extraordinary times:
- Place all monitoring and communication with suppliers on high alert. This is not the time to “leave well enough alone”. Be proactive with frequent communication – especially with distant and historically problematic suppliers -- and maintain an interest in the general state of their business including their work level with other customers.
- Ask your suppliers if they have received PPP funds. If so, determine when they run out and if layoffs are anticipated at that time.
- Be especially sensitive to supplier personnel changes and push to understand why changes are made and what impact they have as soon as you are aware of them.
- Utilize outside reporting services to monitor suppliers’ payment patterns to their vendors. If you are not familiar with this process, check with your company’s credit department. Your company might already subscribe to a service that can easily provide this information. Note any sudden increase in time-to-pay which can be an early indicator of financial problems.
- Keep track of inter-state and international travel restrictions. A simple spreadsheet with suppliers by state (and country) can help evaluate news of changing restrictions as it arises. Set up an alert at google.com/alerts using “covid-19 travel restrictions” to receive daily updates via email on any new or changing restrictions.
- If your company allows travel – identify which individuals in your company are willing and able to travel. It might not be the same people you have relied upon in the past.
- If your company requires that business travel is only for essential purposes, make sure you know what the authorization chain is for such approval before the need arises.
- If your company has divisions in other states, familiarize yourself with their procurement organizations in case you need to reach out for local assistance.
- Consider using third party procurement service companies that can get you localized help at supplier facilities on an as-needed basis.
These are extraordinary times. Never have supply chains been so fragile, and never has in-person response to supplier emergencies been so logistically difficult. It is important for supply chain professionals – especially those at OEM’s that have been enjoying good supplier performance due to temporary government support programs at their suppliers – to be on high alert for supplier problems and to have contingencies in place for getting boots on the ground where needed.